Description
Related information about LYD105A HITACHI control module:
Product Description
LYD105A is a high-performance industrial control module launched by Hitachi,designed for AC drive inverters.This module is mainly used in industrial automation control systems,which can receive input signals,process data,and generate output signals to achieve precise control of external devices or systems.
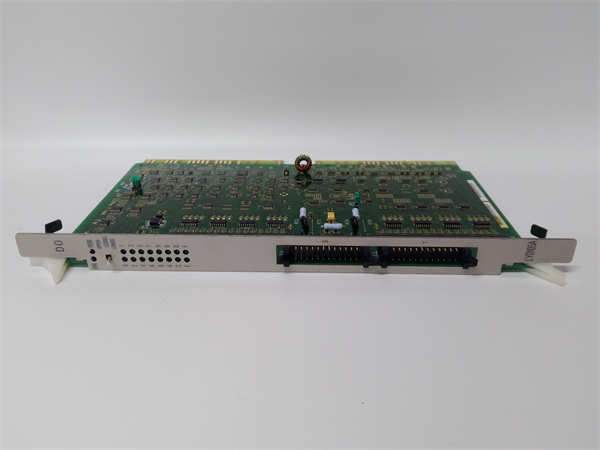
LYD105A HITACHI
Product parameters
model:LYD105A
Power:7.5hp or 5hp.
Input voltage range:200-240V AC or 380-480V AC.
Frequency range:0-500Hz or 0.1-60Hz.
Protection function:equipped with overload protection,overvoltage protection,and undervoltage protection.
Communication interface:RS-485、Ethernet、Modbus RTU。
Control modes:vector control,scalar control.
Product specifications
Control specifications:Supports multiple control modes such as vector control and scalar control,and can adapt to different motor control requirements.
Protection specifications:Some products have a protection level of IP55,which can effectively prevent dust and water.
Communication specifications:Supports multiple communication protocols for easy connection and data exchange with other devices.
series
Belongs to the Hitachi control system series.
features
Accurate control:Advanced vector control technology is adopted to ensure smooth and precise operation of the motor at different speeds.
High reliability:Equipped with multiple protection mechanisms such as overload,overvoltage,undervoltage,etc.,it can effectively extend the service life of the equipment.
Strong compatibility:Supports multiple communication interfaces and protocols,and can be integrated into control systems with various devices.
Easy to operate:With a user-friendly interface,parameter settings and monitoring can be performed through the control panel or remote interface.
Wide adaptability:The working temperature range is wide and can adapt to extreme industrial environments ranging from-40℃to+85℃.
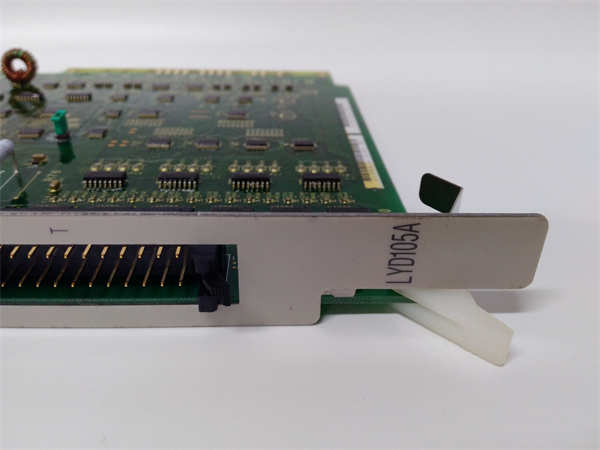
LYD105A HITACHI
effect
Motor control:Accurately control the speed,torque,and other parameters of the motor to achieve smooth starting,stopping,and speed regulation of the motor.
System integration:It can serve as the core component of industrial automation systems and work in conjunction with devices such as PLCs,sensors,and actuators.
Fault protection:Real time monitoring of equipment operation status,timely cutting off of circuits when abnormalities occur,protecting equipment and personnel safety.
purpose
Energy saving optimization:Automatically adjust the motor operation status according to load demand,reduce energy consumption,and achieve energy-saving goals.
Process control:In industrial production processes,precise control of various motor driven equipment is carried out to ensure the stability and consistency of the production process.
Equipment monitoring:Real time monitoring of motor and equipment operating parameters,providing data support for equipment maintenance and fault diagnosis.
application area
Manufacturing industry:used for controlling robots,conveyor belts,machine tools and other equipment in automated production lines such as automobile manufacturing and electronic equipment production.
Logistics industry:Efficient handling and storage of goods in logistics equipment such as automatic sorting systems and intelligent warehouse management systems.
Energy industry:Control ventilation and cooling equipment in power plants,as well as coal transportation equipment in substations.
Water treatment industry:used for motor control of water pumps,aeration equipment,etc.in sewage treatment plants and waterworks.